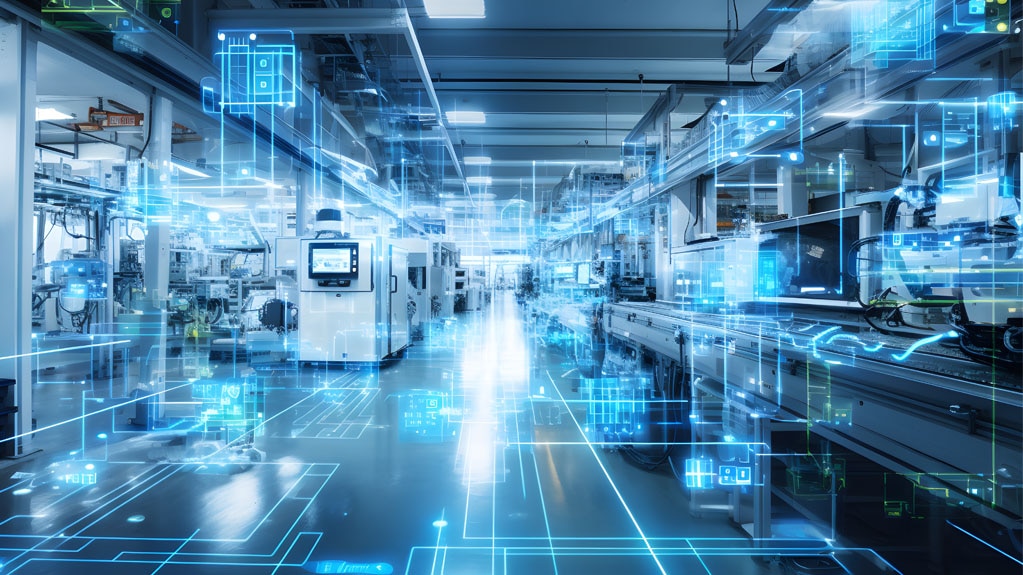
【完全ガイド】スマートファクトリーの基礎知識から導入方法、活用できる補助金まで
デジタル技術の進化に伴い、製造業の生産性や競争力を向上させる「スマートファクトリー」が注目を集めています。スマートファクトリーは、IoTを活用して工場の各プロセスをデータ化し、AIなどを用いながら分析することで、効率的かつ柔軟な生産体制を実現するものです。
この記事では、スマートファクトリーの基本概念や導入によるメリット、具体的な導入プロセス、導入時の課題と対策について詳しく解説します。日本政府が推進する「スマートファクトリーロードマップ」に基づき、製造業が直面する課題を解決し、持続的な成長を目指すための戦略を探っていきましょう。
目次[非表示]
スマートファクトリーの基本概念
まずは、スマートファクトリーの定義や従来の工場との違い、「インダストリー4.0」との違いについて説明します。
スマートファクトリーの定義とは
グローバル競争の激化や人手不足、環境規制の強化など製造業の直面する課題が年々複雑化しており、従来の生産方式では対処しきれない状況が続いています。そのため、工場や生産ラインにおけるデジタル化・効率化は急務です。
このような状況で注目されているのが、スマートファクトリーという新しい工場の概念です。スマートファクトリーは、工場の各プロセスや機器をネットワークで連携させ、IoT(モノのインターネット)やAI(人工知能)などの最新技術を活用してデータをリアルタイムに収集・分析することで、生産効率を最大限に引き上げることを目指しています。
従来の工場との違い
従来の工場は、個々の機械や設備が独立して稼働しており、各プロセスのデータ収集や管理は現場にいる担当者が手作業で行うなど、アナログな方法に依存していました。集めたデータの連携も表計算ソフトなどを使って手動で行うほかなく、工場の生産性を見直すためには、大きな手間を要します。
スマートファクトリーでは、IoTやAIにより各機械や設備がリアルタイムで情報を共有できるため、非効率な手作業でのデータ収集・連携の必要がなくなります。生産ライン全体の稼働状況や設備の状態が可視化されるので、異常発生時の瞬時のアラートや予知保全も可能です。
さらに、リアルタイムで蓄積されたデータは、AIを用いて生産計画やメンテナンスの最適化に役立てることもできます。こうした仕組みにより従来の工場と比べて、生産性向上や効率化が飛躍的に改善されるのです。
スマートファクトリーとインダストリー4.0の関係
スマートファクトリーの基本的なコンセプトは、ドイツ政府が提唱する「インダストリー4.0(第4次産業革命)」から始まりました。インダストリー4.0とは、製造プロセスを自動化・効率化することで、生産の柔軟性と効率を飛躍的に向上させる産業政策で、以下4つの設計原則があります。
- 相互運用性:モノ・人・システムなど生産に関連する全てをつなぎ、さまざまなセンサー・デバイスを連携させたリアルタイムなデータ収集で、自律的な意思決定を可能にする。
- 情報の透明性:集めたデータをもとに仮想モデルを作成・可視化し、製品開発や需要の分析などに活用する。
- 技術的アシスト:センサーやデバイスでデータ収集をサポートし、重労働や危険な作業を産業ロボットで代替する。
- 分散型意思決定:収集したデータをサイバー空間で分析し、現実世界へフィードバックする仕組みを用いて、生産ラインの意思決定をできる限り自律化させる。
これらをIoTやAI、クラウドコンピューティング、拡張現実(AR)などの先進技術を用いることで、20世紀後半の第3次産業革命(デジタル革命)に続く変革を起こそうとしています。
製造業が盛んなドイツですが、近年ではアジア諸国の技術力向上による短納期・高品質・低価格の製品が世界に供給されていることに危機感を感じていました。グローバル市場で優位性を確保するため、より少ない労力で多くの製品を生産できるよう効率アップすることでシェア拡大を目指しています。
ドイツのインダストリー4.0に続き、アメリカの「Industrial Internet Consortium(IIC)」や日本の「スマートファクトリーロードマップ」など、世界各国で製造業のデジタル化・IoT化に向けた動きが加速しているのが現状です。
スマートファクトリーの5つのメリット
スマートファクトリーの導入は、製造業において多くのメリットをもたらします。なかでも代表的な5つのメリットをご紹介します。
生産性の向上
ロボット技術の活用により、作業の自動化や省力化を実現可能です。また、IoTを活用して生産プロセス全体を可視化することで、工場内の各プロセスや設備の状態をリアルタイムで監視・分析し、非効率な部分を特定し最適化できます。
これにより稼働率の向上や生産サイクルの短縮を実現でき、工場全体の効率を高められます。
コストの削減
テクノロジーの活用で生産プロセスの最適化が図られるため、材料やエネルギーの無駄を削減でき、コスト効率が向上します。例えば、AIを活用して生産計画を自動調整することで、過剰な材料使用や在庫の余剰を防ぎ、リソースを適正に管理できます。
また、予知保全技術では、設備に取り付けられたセンサーが温度・振動・音など設備の稼働状態をリアルタイムで監視し、異常が発生する兆候を検知可能です。例えば、振動センサーが異常な振動を検知すると、AIがデータを分析し、部品の摩耗や故障の可能性を早期に判断します。
実際に故障が発生する前にメンテナンスすべきタイミングを把握できるので、適切な対策を講じることができ、突発的な故障による稼働停止を未然に防げます。メンテナンスコストや生産ライン停止による損失を最小限に抑えることが可能です。
品質の向上
スマートファクトリーでは、IoTやAIを使って生産データを収集・分析し、製品の品質をリアルタイムで監視できます。これにより、製造工程で発生するばらつきを最小限に抑え、不良品の発生率を低減します。
また、センサーによるモニタリングで、設備や材料の状態を細かく監視し、異常が発生した場合にはすぐに対応できるため、安定した品質を維持することが可能です。
人手不足の解消
少子高齢化による労働力不足に直面する製造業において、人手不足の解消に大きく貢献します。従来の工場では、熟練技術者の経験や勘に頼った属人的な作業が多く、技術継承が課題となっていました。
スマートファクトリーでは、IoTやAIを活用して作業データを収集・分析し、ベテラン技術者のノウハウをデジタル化できるため、効率的な技術の継承が可能です。
また、データを活用して各プロセスを効率化することで、一部作業を完全自動化し、人手に頼らない生産体制を構築することも期待されています。
リスク管理の強化
スマートファクトリーでは、センサーやモニタリング技術を使って製造プロセス全体を監視できるため、設備の異常やトラブルを早期に発見・対処できます。
また、データを分析することで、リスク要因を事前に特定し、未然に防ぐことも可能です。予期せぬダウンタイムや不良品の発生を最小限に抑えられるので、安定した生産体制を維持できます。不良品の出荷や製造過程での事故などを防止することで、社会的な信用の損失を防ぐことにもつながります。
スマートファクトリーの導入プロセス
スマートファクトリーの導入には、企業の業務プロセスをデジタル化し、効率的な生産体制を整えるために、段階的なステップが必要です。一般的な導入プロセスの流れを紹介します。
現状分析と目標設定
導入の第一歩は、工場や生産ラインの現状を正確に把握し、改善すべきポイントを特定することです。
企業が抱える課題(生産性の低下、コスト増大、品質のばらつきなど)を整理し、スマートファクトリー導入によってどのような成果を得たいのか、具体的な目標を設定します。これにより、導入プロジェクトの方向性が明確になります。
また、全社的なデジタル化に対する意識共有や、経営層のサポートを得ることも重要な要素です。導入にあたっての目標として、以下のような具体的な指標を設定します。
|
テクノロジーの選定とインフラ整備
目標を設定したら、スマートファクトリーの実現に必要なテクノロジーを選定します。IoTデバイス、センサー、クラウドコンピューティング、AI(人工知能)、ビッグデータ解析など、さまざまなデジタル技術の中から、企業のニーズに合ったものを導入します。特に、リアルタイムでデータを収集・分析できるシステムの構築が重要です。
さらに、デジタル化されたデータを一元管理するためのインフラ整備も不可欠です。これには、工場全体をネットワークで接続するための通信インフラや、データを保存・処理するクラウド環境の整備が含まれます。しっかりとインフラを整備することで、工場全体のデータがリアルタイムで共有され、スマートファクトリーの基盤が整います。
スモールスタートで導入
スマートファクトリーをいきなり全社的に導入するのではなく、まずは一部工場や生産拠点などからスモールスタートさせるのが一般的です。
スモールスタートとは、時間・予算をかけて大がかりな準備をするのではなく、小さい規模で素早くスタートさせる考え方です。小規模に開始することで大きく予算・リソースを割いて失敗するリスクを抑えるとともに、現場の混乱を最小限にとどめます。
取り組みの範囲が限定的なため管理しやすいのもメリットで、スモールスタートにより得たノウハウをもとに、本格的な全社的な展開を行いやすくなります。
パイロットプロジェクトの実施と効果検証
次に、実際に運用するにあたって発生し得る問題点の検証のためパイロットプロジェクト(試験運用)を実施しましょう。小規模なラインや一部の設備を対象に試験運用を行い、技術的な課題や改善点を確認します。例えば、特定の生産ラインにセンサーを設置し、リアルタイムでデータを収集・分析することで、どのような業務改善が可能か検証します。
また、運用するにあたってどのような問題・課題が発生するのかを検証し、本格的な運用時に改善して精度を高めるのも目的です。
パイロットプロジェクトの効果検証は、定量的な指標(生産性・品質・コストなど)と定性的な指標(従業員の反応・作業の容易さなど)の両面から評価し、ここで得られた結果をもとに、次のステップである全体への展開が適切かどうかを評価します。
全社的な展開と最適化
パイロットプロジェクトの成功を確認した後は、全社的にスマートファクトリーを展開していきます。各工場や生産ラインにIoTやAIを導入し、生産管理システムとの連携を進めます。
重要なのは、各プロセスがデータに基づいて最適化され、継続的な改善サイクルを回せるようにすることです。
運用後のモニタリングと改善
仕組みを一度導入すれば完了というわけではなく、運用後もデータを活用した継続的なモニタリングと改善が求められます。導入したシステムが適切に機能しているか、目標とする成果が得られているか確認し、PDCAサイクルを短いスパンで回しながら必要に応じて調整を行います。
さらに、経済産業省が策定した「スマートファクトリーロードマップ」において、ものづくりのスマート化をさらに展開させるには、大きく3つの方向性があると指摘されています。
- 方向性①データの高度活用:データをさらに高度に活用し、導入効果の向上を追求します。PDCAサイクルによって蓄積されたデータを分析し、生産性や効率性を向上させるための最適化が継続的に行われます。
- 方向性②システムの横展開:導入したシステムを単一のプロセスやラインに留めず、工場全体や他の拠点に横展開します。導入効果を面的に拡大していくことで、生産拠点全体の効率化が進みます。
- 方向性③システムの応用と多目的化:導入したシステムを他の目的にも応用します。IoTやAIを活用すれば、メンテナンスの予測や生産計画の最適化、サプライチェーンの効率化、環境負荷低減など多岐にわたる改善が可能になります。
PDCAサイクルを軸にした運用後の改善は、システムの進化と効果拡大を継続的に図る重要なプロセスです。スマートファクトリーの導入は、導入しただけで完了するものではなく、段階的な進化と改善を繰り返しながら、その効果を最大限に引き出すことが求められます。
スマートファクトリー導入の課題と対策
スマートファクトリーの導入は大きなメリットをもたらす一方で、いくつかの課題が伴います。ここでは、スマートファクトリー導入に際してよく挙げられる課題と対策を解説します。
初期投資コストの高さ
スマートファクトリーの導入には、センサーやIoT機器、AIシステム、クラウドインフラなどの技術投資が必要です。そのため、初期投資コストが高額になることが企業の大きな課題の一つです。
対策としては、段階的に導入を進めるスモールスタートが有効です。特定のラインや一部の工場からスタートし、成功を確認した後に全社的な展開を行うことで、コストとリスクを低減させることが可能です。
また、政府や自治体が提供するデジタル化促進のための助成金や補助金を活用することも、コストを抑えるための手段となります。
技術の複雑さと対応可能な人材の不足
スマートファクトリーは、IoTやAI、ビッグデータなどの高度なデジタル技術を駆使しますが、多くの企業で技術を理解・運用できるスキルを持った人材が不足しているのも大きな課題です。
対策としては、社内でのデジタルスキルの向上を目的とした研修プログラムの実施が推奨されます。
導入当初は既存の従業員に負担をかけすぎないように、簡単で誰でも使いやすいシステムを選択し、徐々に高度な技術を習得させる環境を整えることが重要です。
また、製造業のDXやサステナビリティ経営に詳しい外部の専門コンサルタントやテクノロジーパートナーとの連携も効果的です。
データセキュリティの確保
工場内のデバイスや機器がインターネットで繋がるため、外部からのサイバー攻撃によるデータの漏洩や、設備の不正操作など、セキュリティリスクが高まる懸念があります。
対策としては、強固なネットワークセキュリティの確保が必要です。暗号化技術やファイアウォール、侵入検知システムの導入により、不正アクセスやデータの漏洩を防ぐ必要があります。
また、研修をはじめ社内でのセキュリティ教育を徹底し、情報の取り扱いに関する適切な知識などを身に付けさせ、普段からセキュリティ意識を高めておくことが重要です。
既存システムとの統合の難しさ
既に稼働している古い設備やシステムと、最新のIoTデバイスやAIシステムを統合することが難しいのも課題です。
対策としては、レトロフィット(既存設備の部分的改修)や、既存システムにIoT対応のセンサーを後付けで追加する方法が有効です。設備全体を新しいものに置き換えることなく、段階的にスマートファクトリー化を進められるので、コストを抑えるとともに稼働停止による損失や従業員の反発を最低限にできます。
また、システムインテグレーター(SIer)と連携して、既存の生産管理システムと新しいデジタル技術をスムーズに統合するためのソリューションを導入することも有効です。
従業員の抵抗と変革への適応
スマートファクトリーの導入は、従業員の働き方や役割を大きく変えることがあるため、技術の急速な進歩への適応に不安を感じる従業員からの抵抗・反発が課題となる場合があります。
対策としては、従業員への十分な説明と研修を行い、スマートファクトリーのメリットを共有することが重要です。
また、従業員が新しい技術に適応するためのサポート体制を整えたり、徐々に変革を進めていったりすることで、段階的に順応できるようにすると抵抗を最小限に抑えられます。企業の中で「変革への適応」を文化として定着させるための組織的な取り組みも効果的です。例えば、従業員のリスキリング(再教育)プログラムや、部門横断型のプロジェクトチームの編成が効果的です。
|
こうした取り組みで従業員の苦手意識・拒否反応を薄めるとともに、経営層から積極的に変革の目的やメリットを明確に伝えることで、従業員の理解と協力を得られます。
政府の取り組みとロードマップ
日本政府は、製造業の国際競争力を強化するためにスマートファクトリーの導入を積極的に推進しています。
スマートファクトリーロードマップの概要
経済産業省による「スマートファクトリーロードマップ」は、日本の製造業をデジタル化し、製造業の生産効率と品質を向上させることで、国際競争力を強化し持続可能な成長を実現するために策定されました。
具体的には、製造プロセス全体のデータを活用し予測・最適化を行うことで、無駄を減らした効率的かつ柔軟な生産体制を確立することが目指されています。
スマートファクトリーロードマップは、次の3つの段階を踏んで、製造業のスマート化を推進します。
|
スマートファクトリー推進政策
スマートファクトリー導入を促進するため、日本政府や地方自治体は、さまざまな補助金制度を提供しています。中小企業を中心に、スマート化を進めるための設備投資や技術導入を支援するもので、企業が生産性向上を目指すための強力なサポートとなります。
以下は代表的な補助金制度の概要です。
ものづくり補助金(ものづくり・商業・サービス生産性向上促進補助金)
通称「ものづくり補助金」は、中小企業を対象とした補助金制度で、製造業やサービス業の生産性向上に必要な設備投資や技術導入に活用できます。新製品や新サービスの開発支援に加え、海外展開を目指す事業にも対応するなど、幅広い企業活動に適用可能です。
- 補助金上限:一般型1,000万円、グローバル型3,000万円
- 補助率:中小企業1/2、小規模事業者2/3
成長型中小企業等研究開発支援事業(Go-Tech事業)
中小企業が大学や公設試験研究機関などと連携して行う、研究開発や試作品開発、そしてその事業化に向けた活動を支援する補助金制度です。特定のものづくり基盤技術やサービスの高度化を目指す中小企業に対して、最大3年間の支援を提供します。
2022年度より、これまでの「戦略的基盤技術高度化支援事業(サポイン事業)」や「商業・サービス競争力強化連携支援事業(サビサポ事業)」が統合され、Go-Tech事業として一本化されました。これにより、より多様な技術・事業分野でのイノベーションが期待されています。
- 補助金上限:単年度あたり4,500万円、2年間合計7,500万円、3年間合計9,750万円(通常枠)、3年間合計3億円(出資獲得枠)
- 補助率:中小企業は2/3以内、大学・公設試等は定額
IT導入補助金(サービス等生産性向上IT導入支援補助金)
ITツールを導入して生産性を向上させるために利用できる制度です。特定のITツールの導入を支援しており、ソフトウェアやIT関連の費用に対して補助が受けられます。
- 補助金上限:450万円
- 補助率:1/2
スマート社会実装化促進事業補助金
京都府内の中小企業などを対象に、超スマート社会の実現を目指した新たなサービスや技術の開発に必要な経費の一部を補助する制度です。ICTなどの先端技術を活用し、脱炭素社会や快適な社会生活の実現に向けたイノベーションの創出を支援します。
- 補助金上限:500万円
- 補助率:1/2以内これらの補助金を活用することで、設備投資にかかる負担を軽減し、デジタル化を加速させることが可能です。
いずれの補助金も一定の条件を満たす必要があるので、自社がどの補助金の対象となるか確認しましょう。
また、スマート社会実装化促進事業補助金のように、自治体単位で行っている補助金制度もあるため、自社が属する自治体の補助金情報も確認することも大切です。
条件の把握や申請書類の作成が難しい場合は、外部のコンサルタントなどに依頼するのもおすすめです。
特に、経済産業省は「スマートファクトリーロードマップ」を発表し、日本の製造業がデジタルトランスフォーメーション(DX)を通じて持続可能な成長を遂げるための具体的な指針を示しています。日本企業が国際的に競争力を高め、産業全体の効率化と持続可能性の実現を目指しています。
まとめ
スマートファクトリーの導入は、製造業にとって欠かせないデジタルトランスフォーメーション(DX)戦略の一環として、重要性を増しています。企業は生産性向上やコスト削減、品質の向上を実現でき、少子高齢化やグローバル競争に直面する製造業の競争力強化が期待されています。
日本政府も「スマートファクトリーロードマップ」を策定し、製造業全体のデジタル化を推進してきました。中小企業への補助金制度や、デジタル技術の習得支援プログラムなど、企業がスマートファクトリーを導入しやすい環境が整えられています。
しかし、スマートファクトリーの導入には、技術的な複雑さや高額な初期投資、社内のスキル不足など課題も伴います。
フューチャーアーティザン株式会社では、データ活用基盤「YDC SONAR」、AI画像解析サービス「SearchMaru」やスマートファクトリー化のサービス「Future Artisan Smart Factory 」を展開しています。スマートファクトリーの資料をはじめ各種カタログ・ホワイトペーパーをご用意しているので、まずはお気軽にダウンロードください。