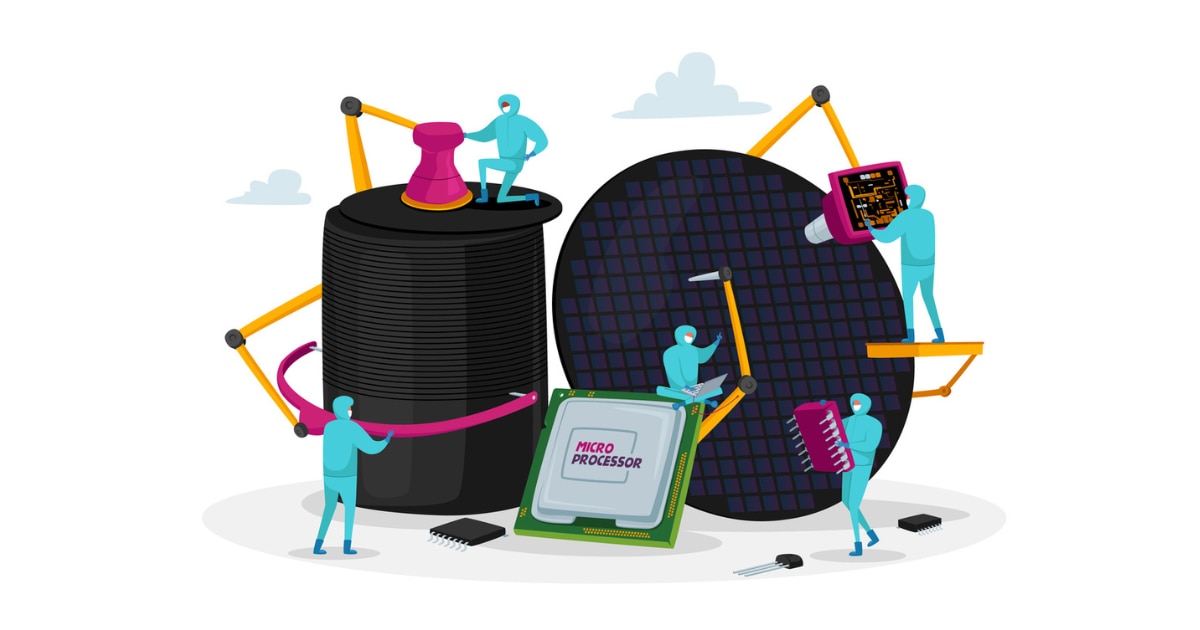
半導体ウエハ検査とは?半導体の検査装置とAI活用の違いとAI事例
目次[非表示]
- ・半導体ウエハ検査とは?
- ・半導体ウエハ検査の主な検査工程をわかりやすく解説
- ・1. 外観検査(Visual Inspection)
- ・2. 前工程検査(Pre-process Inspection)
- ・3. 電気的検査(Electrical Testing)
- ・4. ダイ・テスト(Die Test)
- ・5. 後工程検査(Post-process Inspection)
- ・6. 環境試験(Environmental Testing)
- ・7. 最終検査(Final Test)
- ・半導体ウエハ検査の主な検査項目一覧
- ・1. 外観検査(Visual Inspection)
- ・2. 電気的検査(Electrical Testing)
- ・3. 検査プローブテスト(Probe Testing)
- ・4. ダイ(チップ)テスト(Die Test)
- ・5. 厚さ測定(Thickness Measurement)
- ・6. 膜厚測定(Film Thickness Measurement)
- ・7. レジストパターン検査(Resist Pattern Inspection)
- ・8. 不良ピン検査(Pin Inspection)
- ・9. 絶縁性検査(Insulation Testing)
- ・10. 金属間の接続検査(Intermetallic Bonding Test)
- ・11. ワイヤーボンディング検査(Wire Bonding Inspection)
- ・12. パッケージング後検査(Post-packaging Inspection)
- ・13.最終性能テスト(Final Performance Test)
- ・半導体ウエハ検査の主な方法
- ・AIを活用した半導体ウエハ検査の検査事例
- ・おすすめのAI画像検査システム「SearchMaru」
半導体ウエハ検査とは?
半導体ウエハ検査とは、半導体デバイスが製造される際に使用されるウエハ(薄い円盤状の基板)に施される検査のことです。半導体製造は微細な回路をウエハ上に作り込む工程であり、その品質や精度が最終製品の性能に大きく影響します。ウエハ検査の目的は、製造過程で発生した微小な欠陥を検出し、デバイスとして不良品を市場に出さないことです。検査には多くの段階があり、ウエハ表面の状態をチェックしたり、回路の不具合や不良を特定したりするためにさまざまな技術が駆使されます。近年では、AI技術を利用した検査が導入され、検査精度の向上や効率化が進んでいます。
半導体ウエハ検査の主な検査工程をわかりやすく解説
半導体ウエハ検査は、製造された半導体チップ(集積回路)が正常に機能するかどうかを確認する重要な工程です。ウエハ(シリコンの基板)の上に多数のチップが並んでおり、その一つ一つが最終製品となるため、検査は非常に慎重かつ正確に行う必要があります。主な検査工程について、以下のとおり解説します。
1. 外観検査(Visual Inspection)
この工程では、ウエハの表面を目視や機械的手段で検査します。主に以下の点を確認します。
|
▼半導体ウエハのAI画像検査に関するPDF資料
AI外観検査システムを導入するときに検討すべき22の比較項目
半導体ウエハに対応した
AI外観検査「SearchMaru」
2. 前工程検査(Pre-process Inspection)
ウエハが製造される過程の初期段階で行う検査です。シリコンウエハが適切に準備されているか、エッチングや薄膜形成の前に重要な特性を確認します。これにより、後の工程での不良を未然に防ぎます。
3. 電気的検査(Electrical Testing)
ウエハ上の各チップの電気的な特性を測定する工程です。主に以下のテストが行われます。
|
4. ダイ・テスト(Die Test)
ウエハの各チップが正常に動作するか、個別にテストします。このテストは、ウエハのダイ(チップ)単位で行われます。ダイ・テストの結果、不良品を早期に発見し、後の工程での無駄を減らすことができます。
5. 後工程検査(Post-process Inspection)
ウエハの後工程(ダイシングやパッケージング)前に、再度検査を行います。
ここでは、次のような検査が含まれます。
|
6. 環境試験(Environmental Testing)
特に高性能や特殊用途の半導体においては、温度や湿度、振動などの環境条件に耐えるかを確認する試験も行われます。これにより、製品が実際の使用条件下でも安定して動作するかを確認します。
7. 最終検査(Final Test)
すべての製造工程が完了した後、最終的に製品が仕様通りであるかどうかを確認します。ここでは、最終的な性能チェックを行い、合格品と不良品を分けます。これらの検査工程を経て、不良品を取り除き、品質の高い半導体チップが市場に出荷されます。検査工程は非常に精密で、各段階で問題があれば次の工程に進む前に修正が行われるため、品質を確保するためには欠かせないステップとなります。
半導体ウエハ検査の主な検査項目一覧
半導体ウエハ検査の主な検査項目は、ウエハの製造過程における品質確認や不良の発見を目的として行われます。各検査項目は、製造の各ステップで不具合を早期に発見し、最終製品の品質を確保するために非常に重要です。以下に、半導体ウエハ検査の主要な検査項目を詳しく解説します。
1. 外観検査(Visual Inspection)
ウエハの表面を肉眼や高倍率の顕微鏡で検査し、以下の欠陥を確認します。
|
▼半導体ウエハのAI画像検査に関するPDF資料
AI外観検査システムを導入するときに検討すべき22の比較項目
半導体ウエハに対応した
AI外観検査「SearchMaru」
2. 電気的検査(Electrical Testing)
半導体チップの電気的な動作を確認するための検査です。具体的には以下の項目が含まれます。
- 開放回路検査(Open Circuit Test): 回路が正常に接続されているかを確認するテスト。回路が開いている場合(接続不良)、信号が流れず、チップは動作しません。
- 短絡回路検査(Short Circuit Test): 回路間に短絡がないかを確認します。短絡が発生すると、過電流が流れ、故障の原因になります。
- スイッチング特性検査:ロジック回路やトランジスタのスイッチング速度、立ち上がり時間、立ち下がり時間などを測定します。
- パラメータ検査:動作電圧、消費電流、抵抗、インピーダンスなどの電気的パラメータを測定し、製品の仕様を満たしているかを確認します。
3. 検査プローブテスト(Probe Testing)
ウエハ上の個々のチップに対して、直接プローブを接触させて電気的な動作を確認するテストです。
|
4. ダイ(チップ)テスト(Die Test)
ウエハ上の個別のチップ(ダイ)に対して、以下のテストが行われます。
|
5. 厚さ測定(Thickness Measurement)
ウエハの厚さを測定し、製造プロセスでの均一性を確認します。ウエハの厚さが不均一だと、後工程でのダイシングやパッケージングで問題が発生する可能性があります。
6. 膜厚測定(Film Thickness Measurement)
ウエハ上に形成された薄膜(絶縁膜、導電膜、半導体膜など)の厚さを測定します。膜の厚さが規定値から逸脱していると、回路の動作に影響を与える可能性があるため、正確な膜厚が要求されます。
7. レジストパターン検査(Resist Pattern Inspection)
8. 不良ピン検査(Pin Inspection)
各チップの端子(ピン)が正常に接続されているか、またはピンの形状が正しいかを確認する検査です。ピンが正しくない場合、接続不良が起こり、チップが動作しません。
9. 絶縁性検査(Insulation Testing)
ウエハ上の各回路間に適切な絶縁が施されているかを確認します。絶縁が不十分だと、異常な電流が流れ、ショートや故障を引き起こす可能性があります。
10. 金属間の接続検査(Intermetallic Bonding Test)
金属層間の接続状態を検査します。半導体デバイスは複数の金属層で構成されており、これらの接続が強固でないと、デバイスが破損したり、動作不良を引き起こしたりします。
11. ワイヤーボンディング検査(Wire Bonding Inspection)
ウエハ上のチップと外部回路との接続に用いられるワイヤーボンド(細い金属線)の接続状態を確認します。ボンディング不良があると、接続不良が発生し、回路が機能しなくなります。
12. パッケージング後検査(Post-packaging Inspection)
ウエハがダイシングされ、チップがパッケージに封入された後に行われる検査です。パッケージに異常がないか、リードフレームの接続状態やパッケージの密封状態を確認します。
13.最終性能テスト(Final Performance Test)
最終的に製品が仕様通りの性能を発揮しているかを確認するテストです。例えば、動作速度、消費電力、動作温度範囲などが設計通りかどうかを確認します。
これらの検査項目は、半導体の製造工程における品質管理の重要な部分を担っており、最終的な製品の信頼性や性能に大きな影響を与えます。各項目を順次クリアしていくことで、高品質な半導体製品を提供できるようになります。
半導体ウエハ検査の主な方法
半導体ウエハ検査には多くの方法があり、それぞれ異なる検査項目に対応しています。本コラムでは、外観検査やAI画像検査について紹介します。
半導体検査装置で検査する
外観検査装置は、ウエハ表面の目に見える欠陥(例えば、傷や汚れ、異物など)を確認するためのシステムです。外観検査装置は通常、カメラやCCDセンサー、顕微鏡機能を備えており、ウエハ表面を高精度で検査します。高解像度で表面の微細な欠陥を検出することができます。
代表的な技術
- カメラベース検査:高解像度カメラを使用して、ウエハ表面の欠陥を撮影し、欠陥位置や形状を検出します。
- 非接触型検査:物理的にウエハに接触せず、非接触で欠陥を検出する方法です。
AI画像検査で検査する
AI画像検査は、コンピュータビジョンと機械学習アルゴリズムを使用して、ウエハ表面の欠陥を検出します。AIは大量のデータを学習し、欠陥の種類やパターンを識別する能力を持っています。これにより、従来の画像処理システムでは検出できなかった微細な欠陥や異常を見逃さずに検出することができます。
深層学習(Deep Learning):複雑な欠陥を検出するために、深層ニューラルネットワークを使用した検査技術です。これにより、品質チェックの精度が向上します。
畳み込みニューラルネットワーク(CNN): 画像認識技術の一つで、ウエハ表面の異常を自動的に識別します。
特徴的な技術
- 深層学習(Deep Learning):複雑な欠陥を検出するために、深層ニューラルネットワークを使用した検査技術です。これにより、品質チェックの精度が向上します。
- 畳み込みニューラルネットワーク(CNN): 画像認識技術の一つで、ウエハ表面の異常を自動的に識別します。
▼半導体ウエハのAI画像検査に関するPDF資料
AI外観検査システムを導入するときに検討すべき22の比較項目
半導体ウエハに対応した
AI外観検査「SearchMaru」
2つの方法のメリットとデメリット
半導体ウエハ検査における半導体外観検査装置(通常は高解像度のカメラや顕微鏡を使用)とAI画像検査(人工知能を用いた画像解析)のそれぞれのメリットとデメリットについて詳しく説明します。
メリット | デメリット | |
外観検査装置 |
|
|
AI画像検査 |
|
|
最終的には、半導体ウエハ検査の目的や規模、使用する設備によって、どの検査方法を選択するかが決まります。多くの場合、外観検査装置とAI画像検査を組み合わせて使用することが効果的です。外観検査装置での初期的なチェックと、AIを活用した高度な欠陥検出を組み合わせることで、検査精度と効率を最大限に引き出すことができます。
AIを活用した半導体ウエハ検査の検査事例
AIを活用した半導体ウエハ検査は、半導体製造工程での欠陥検出や品質管理において革新的な方法となっています。特に、AI技術(特にディープラーニングや畳み込みニューラルネットワークCNN)が、半導体ウエハ上の微細な欠陥を高精度で検出できるため、製造の効率向上と高い品質基準の維持に貢献しています。以下は、AIを活用した半導体ウエハ検査のいくつかの実際の事例です。
1. ウエハ表面の外観検査(欠陥検出)
事例概要 AIを用いた外観検査では、ウエハ表面の欠陥(傷、異物、汚れ、パターン不良など)を高精度で検出します。特に、ディープラーニングモデルは、ウエハ表面の画像を分析し、微細な欠陥を従来の方法よりも優れた精度で識別できます。 | |
検査内容
| |
メリット
| |
実際の事例 ある半導体製造メーカーでは、AIを使った検査システムを導入し、ウエハ表面に現れる微細なパターン不良を検出しています。このシステムは、数百万枚に及ぶウエハ画像データを学習し、製造ラインで発生する可能性のある多種多様な欠陥を自動的に識別します。特に、目視では見逃しやすい小さな傷や異物を迅速に検出することができ、品質向上に寄与しています。 |
2. パターン転写の不良検出(フォトリソグラフィー検査)
事例概要 フォトリソグラフィー工程では、レジストパターンがウエハ上に転写されますが、転写精度が不完全な場合、欠陥が発生します。AIは、この転写パターンの品質をチェックし、精度を高めるための重要な役割を担います。 | |
検査内容
| |
メリット
| |
実際の事例 ある半導体メーカーでは、AIを使ってフォトリソグラフィー工程のパターン転写精度を検証しています。このシステムは、パターンの転写不良をリアルタイムで発見し、製造中の問題を早期に指摘します。特に微細なパターンのズレや欠落を検出することができ、製造効率と製品品質の向上に貢献しています。 |
3. ワイヤーボンディング不良検出
事例概要 ウエハチップのワイヤーボンディング工程では、ワイヤーが不適切に接続されることがあり、これが製品の不良を引き起こします。AIはワイヤーボンディング不良を自動で検出することができます。 | |
検査内容
| |
メリット
| |
実際の事例 AIによるワイヤーボンディング不良検出システムを導入した半導体メーカーでは、ボンディング工程で発生する微細な不良を迅速に検出できるようになり、不良品の出荷を防ぐことができています。このシステムは、ワイヤーの位置ずれや断裂、接続不良を高精度で判断し、品質向上に貢献しています。 |
最近、AIを活用した半導体ウエハ検査の実際の事例として、AIが高精度でウエハ上の微細な欠陥を検出するケースが増えています。例えば、以下のような事例があります。
- 欠陥検出:AIによる画像解析により、目視検査では見逃しがちな微細なクラックや微小なパターン不良を高精度に検出。
- 不良品率の低減:AIが過去のデータを学習し、不良品の兆候を早期に察知することで、製造工程での不良品率を大幅に低減。
AI活用による検査事例では、従来の検査方法に比べて、検出精度や効率が大きく向上しており、製品の品質が大幅に改善されています。
▼半導体ウエハのAI画像検査に関するPDF資料
AI外観検査システムを導入するときに検討すべき22の比較項目
半導体ウエハに対応した
AI外観検査「SearchMaru」
おすすめのAI画像検査システム「SearchMaru」
製品概要
「SearchMaru」は、半導体ウエハの検査に特化したAI画像検査システムです。このシステムは、深層学習技術を活用し、ウエハ上の微細な欠陥を高精度で検出します。複雑なパターンや小さな異常も見逃さず、リアルタイムでの検査が可能です。
精度が高くなる理由
「SearchMaru」が高精度で検査できる理由は、深層学習による大量のデータ学習と、AIによる高度な画像解析能力にあります。AIは、過去の検査データを学習し、日々進化し続けるため、検出精度が向上し、未発見の欠陥を検出する能力が向上しています。
「SearchMaru」は、完全自動でウエハをスキャンし、欠陥の有無を判定します。これにより、手作業での確認作業が不要となり、検査時間が大幅に短縮されます。さらに、AIによる継続的な学習により、従来の方法に比べて更に高い効率化が実現可能となります。
このように、半導体ウエハ検査の精度向上と効率化には、AI技術の活用が不可欠です。今後も技術の進化とともに、より高精度かつ効率的な検査が可能になります。