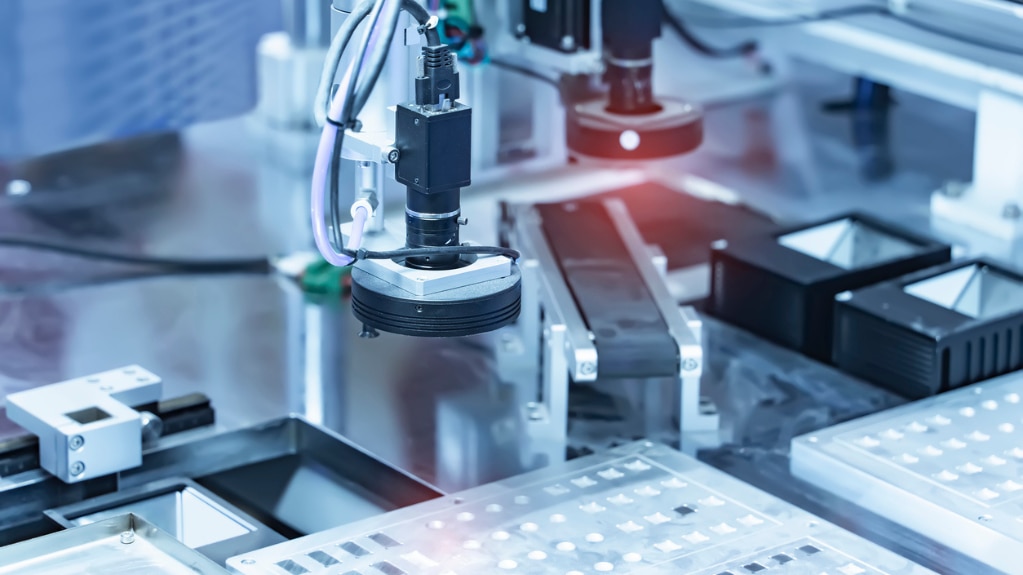
外観検査とは?目的と検査項目、検査方法の種類、AI活用事例を解説
目次[非表示]
製造業の外観検査とは
製品の外観検査とは?意味や定義
外観検査とは、製品の外部を目視またはカメラ、センサーなどを用いて詳細に観察し、製品の品質や異常を確認する重要な品質管理プロセスです。製造ラインにおける中間、または最終チェック工程として、製品の形状、色、傷、汚れ、寸法などを厳密に評価し、不良品を徹底的に排除する役割を担っています。
製造業において、外観検査は単なる品質チェックにとどまらず、企業の信頼性を左右する重要な工程と位置づけられています。不良品の流出は、直接的な経済的損失だけでなく、顧客の信頼を著しく損なう可能性があるため、徹底した外観検査が求められています。
製品外観検査の主な検査項目と検査内容の一覧表
検査項目 |
説明 |
傷の有無 |
|
汚れ・付着物 |
|
変形・歪み |
|
色むら・塗装 |
|
サイズ・寸法 |
|
製品名 |
検査項目 |
半導体ウエハ |
|
電子部品 |
|
自動車部品 |
|
食品 |
|
外観検査の例
外観検査は、さまざまな業界の製品で実施しています。特に、微細な欠陥や高い精度が求められる製品でその効果を発揮します。以下に代表的な例を挙げます。
- 電子機器の部品:基板、コネクタ、トランジスタ
- 自動車部品:エンジン部品、ボディパネル
- 精密機械部品:機械加工部品、金属部品
- 食品・飲料パッケージ:瓶、缶、ラベル
外観検査の目的
外観検査は、製品や部品の外観に異常や欠陥がないかを確認する重要な工程です。この検査の主な目的は、製品が規定通りに製造され、品質基準を満たしていることを保証することです。また、外観検査を通じて製品の信頼性やブランド価値を高め、顧客満足度を向上させる役割も担っています。
品質管理・品質保証の強化
外観検査は、製品の不良品や欠陥を早期に発見し、製造ラインでの問題を早期に改善するために欠かせない工程です。このプロセスを強化することで、製品の品質維持と不良率の低減を図り、最終的には顧客への信頼を築きます。
コスト削減と効率化
外観検査を徹底することで、不良品の発生を抑制し、修理や再生産のコストを削減することができます。早期に不良を発見することで、無駄な生産コストを減らし、効率的な製造が可能になります。
製品の信頼性とブランド価値の向上
高品質な製品を安定して提供することは、企業のブランド価値を高め、顧客の信頼を築く上で重要です。外観検査によって不良品が市場に出るのを防ぎ、製品に対する評価や信頼性を確保することができます。
このように、外観検査は品質維持のために非常に重要な役割を果たしており、その目的は多岐にわたります。
外観検査が難しい理由
外観検査は、製品の見た目に関する細かな検査を行うため、非常に高い精度が求められます。そのため、検査が難しいと感じる理由はいくつかあります。ここでは、その主要な要因について解説します。
判定・評価基準のばらつき
外観検査において最も難しい点は、検査基準が曖昧であり、評価が一貫していない場合があることです。特に目視検査では、作業者の経験や疲労によって判断が異なることが多く、結果として検査精度にばらつきが生じることがあります。このばらつきが製品の品質を不安定にし、改善が難しくなる原因となります。
照明や視覚環境の影響
外観検査は照明条件に大きく影響されます。照明の明るさや色温度、角度などが不適切だと、製品の細かい欠陥や不良が見落とされる可能性があります。また、検査を行う作業環境が整っていないと、視覚的な精度が低下し、誤判定を引き起こすことがあります。
多品種
製品の種類が多品種になればなるほど、検査項目が複雑化し、検査がさらに難しくなります。
例えば、サイズ違いの製品が無数にある場合、サイズのチェックがバリエーションの数だけ必要になり、外観検査が複雑化します。
製造由来の個体差
同じ製品でも、製造ラインや製造装置が異なる場合、製品に微細な個体差が生じることがあります。この差異が外観に現れると、検査員がそれを不良と判断するか、許容範囲として認めるかに迷うことがあり、基準の明確化が難しくなります。
検査対象の規模や数量の多さ
大量生産される製品では、外観検査対象の数が膨大になるため、検査員が一つ一つに十分な時間をかけることができません。そのため、効率的かつ迅速に判定を下す必要があり、ミスを防ぐための十分な注意が必要です。高精度の検査が求められながらも、作業スピードを求められることが、難しさの一因となります。
これらの要因が組み合わさることで、外観検査は非常に高い精度を求められる難易度の高い作業となり、検査工程における課題を引き起こします。
外観検査の検査方法の種類・やり方
外観検査には、さまざまな方法があります。それぞれの方法には特徴や適用できる製品が異なり、検査の精度や効率を高めるために適切な手法を選ぶことが重要です。ここでは、主な外観検査の方法について解説します。
人が目視検査する
どんな検査方法か?
目視検査では、作業者が製品を直接確認し、欠陥や異常を直接チェックします。最も基本的な検査方法ですが、訓練された作業者であれば高い精度を発揮します。
検査精度を高める方法
目視検査の精度を高めるために、いくつかの具体的なアプローチ方法があります。以下に代表的な方法とその効果を説明します。
1.検査員のトレーニングとスキル向上
目視検査は経験と判断力が必要です。定期的なトレーニングやシミュレーションを通じて、検査員が製品の特徴や不良を正確に識別できるようにします。特に、微細な欠陥や複雑な不良を発見するには、検査員の熟練度が重要です。
- 効果:検査員のスキル向上により、不良品の発見が迅速かつ正確になり、品質の一貫性が保たれます。
2.照明条件の最適化
照明の均一性や色温度を調整することで、製品表面の不良が浮き上がりやすくなり、視認性が向上します。適切な照明がないと、欠陥が見えにくくなり、検査ミスが増えます。
- 効果:照明条件を最適化することで、欠陥の見逃しが減り、検査精度が向上します。
3.検査環境の整備
作業台や検査場所を整備し、視界を遮るものがないようにします。使用する機器の点検や、静かな作業環境を提供することで、集中力を高めます。
- 効果:整った環境で検査を行うことで、ミスを減らし、長時間の作業でも高い精度を維持できます。
4.検査結果のフィードバックと改善
定期的に検査結果をレビューし、問題点を分析します。検査員同士で情報共有を行い、改善策を検討します。
- 効果:フィードバックにより、検査員の技術が向上し、全体の検査精度が高まります。
外観検査装置で検査する
外観検査装置は、高度な光学技術とセンサー技術を駆使して、人間の目では捉えきれない微細な欠陥を検出する検査方法です。製造業において、精密かつ高速な品質管理を実現する重要な検査方法として広く活用されています。
どんな検査方法か?
外観検査装置では、高解像度カメラやセンサーを用いて製品の表面を撮影し、その画像データを解析して不良や欠陥を判別します。画像解析や画像処理技術を活用することで、人間の目では見逃しがちな微細な欠陥も検出可能です。
検査精度を高める方法
検査精度を高めるためには、いくつかの具体的なアプローチがあり、それぞれに異なる効果があります。
1.検査装置やツールの精度向上
アプローチ方法:
- 高解像度カメラの使用:解像度を向上させ、微細な欠陥や傷を検出
- 適したレンズの選定:照明や自社製品に最適なカメラのレンズを選定し、精度を高める
- 画像処理技術の活用:高度なアルゴリズムで欠陥を高精度に判定
効果:
- 微細な不良品の見逃し防止
- 検査結果の一貫性が向上
2.照明条件の最適化
アプローチ方法:
均一な照明の確保:光の角度や色温度を調整し、精度向上
照明の種類の選定:LEDや偏光ライトで表面の傷や異常を強調
効果:
検査対象が明確に見え、検査ミスが減少
判断精度が向上
3.定期的なキャリブレーションとメンテナンス
アプローチ方法:
機器のキャリブレーション:定期的に精度を維持
- 定期的なメンテナンス:機器の性能低下を防ぐ
効果:
高精度な検査が長期間可能
- 安定した品質管理が実現
これらのアプローチを組み合わせることで、外観検査の精度は大幅に向上し、製品の品質を高く保つことができます。また、効率性も向上し、コスト削減や生産性の向上にもつながります。
AI外観検査システムで検査する
どんな検査方法か?
AI外観検査システムは、人工知能(AI)を活用して製品の外観を検査する技術で、不良品の発見精度を向上します。従来の目視検査や機械検査に比べ、AIは教示データを学習し、それらの学習データを元に、見逃しを最小限にすることができます。さらに、検査の自動化が進むことで、人手不足や検査員の疲労を減少させ、安定した品質管理が可能となります。
全体を通して「実現できます」のような言い切りが多い。「最小化する」、「実現を目指す」など表現を言い換える必要あり。
✅コラム「AI画像解析とは?できることやメリット、最新の活用事例を紹介」にて詳しく紹介しています。
検査精度を高める方法
1. 高解像度カメラの使用
高解像度のカメラを使用することで、より細かな欠陥を検出できます。カメラの解像度が高ければ、画像データの精度が向上し、AIが欠陥を識別する際の情報量が増えるため、検査精度が向上します。
2. 教示データの充実とチューニング
AIの精度は、教示データに大きく依存します。過去の検査結果や不良品のデータを充実させ、「欠陥の特徴」をもった学習データをAIに学習させることで、AIの判断精度が向上します。製品仕様の変化に応じた継続的なAIのチューニングも不可欠となります。
3. 適切な照明の選定と調整
AI外観検査システムにおいても、照明の条件が重要です。製品や検出したい欠陥の種類により、通常光以外にも紫外線や赤外線などをあてることで、より精度の高い検査が期待できます。照明の角度や明るさを最適化することで、製品表面の微細な欠陥が鮮明に映し出され、AIが正確に検出しやすくなります。
4. 検査結果を素早くフィードバック
AIシステムがリアルタイムで画像を判定することで、、素早いモデルの再学習を可能とします。これにより、判定結果をフィードバックしたをすぐに製造工程へ適用できるので不良品の排除精度がさらに向上します。
これらの方法を組み合わせることで、AI外観検査システムの検査精度は飛躍的に向上し、より高品質な製品を提供することが可能になります。
3つの外観検査手法の違い(メリットとデメリット)
検査方法 |
メリット |
デメリット |
目視検査 |
|
|
外観検査装置 |
|
|
AI外観検査システム |
|
|
これらの手法は、製品の種類や検査の目的に応じて使い分けることが重要です。例えば、簡単な表面の傷や汚れが検査対象であれば目視検査が適していることもありますし、微細な欠陥が多く含まれる高精度な製品検査にはAIや外観検査装置の導入が推奨されます。それぞれの特性を理解し、最適な検査方法を選ぶことが、品質向上に繋がります。
外観検査におけるAI活用の方法とその事例
AI外観検査システム「SearchMaru」とは
「SearchMaru」は、最新のAI技術を活用した外観検査システムで、製品表面の微細な欠陥や不良を高精度で検出することができます。
検査装置から製品の撮像画像または検査画像を受けると、AIで自動的に不良の種別ごとに画像を分類します。分類結果と実績データやプロセス値などと紐づけることにより、不良の要因解析やリアルタイムでの不良検知を実現します。
「SearchMaru 」の特徴
- 画像の学習から導入後のメンテナンス、適応範囲の拡張までお客様で運用可能なオールインワンのサービス
- 生産技術・製造技術・設備技術といった非IT部門の方も簡単に運用できるシンプルな操作と、システム稼働状況も一目でわかる画面仕様
- AIが「どこを」「どのくらいのスコアで」分類したかを可視化するヒートマップと判定スコア表示
- 製品の進捗履歴やプロセスデータ、検査結果データと組み合わせて、不良の発生要因を特定し打ち手をわかりやすくする仕組み
- 1ライセンスで多品種、複数ラインに対応できるコストパフォーマンス
「SearchMaru」の導入事例
今回は、半導体業界のお客様への導入事例をご紹介します。半導体製造工程では、製品の粒度が異なるため欠陥の追跡や原因究明が非常に難しいという課題があります。特に、工程を跨いで発生する欠陥が最終製品に与える影響を事前に予測することは、これまでは困難とされてきました。
●導入前の課題
半導体製造工程では、製品の粒度が異なるため欠陥の追跡や原因究明が難しかった。
欠陥が工程を跨いで発生し、最終製品にどのように影響を与えるかを予測することが困難でした。
●SearchMaru導入後の成果
- 歩留まりが向上
前工程で欠陥が発生した製品を廃棄せず、最終的に不良品となるリスクを予測し、品質向上を実現しました。 - 生産効率の改善
不良品の加工を避けることで、製造の効率化が進みました。
●SearchMaru導入後の各担当者の変化
1. 現場の担当者の変化
- 目視検査による誤判定や精神的負担が軽減しました。
- 品種が変わるタイミングでAIを切り替えるだけで、他の高付加価値業務に時間を割けるようになりました。
- システム部門の変化・データの検索や紐づけ、グラフ化がワンクリックで可能になりました。
- 専門知識がなくても現場で運用でき、業務負担が減少しました。
2. 経営層の変化
- リアルタイムで現場の状況を把握できるようになり、経験や勘に頼らずデータに基づいて最適な判断が可能になりました。
- 業界内で先進的な技術革新を推進しました。
外観検査は品質管理の要であり、AI技術の進化により、人的限界を超える精度と効率を実現します。
SearchMaruは、最新のAI技術で微細な欠陥を高精度に検出し、製造業の品質向上と生産性改善に革新をもたらします。